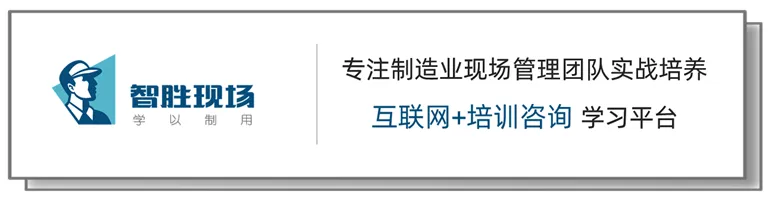
- “维持” 即维持现场稳定,是对现场“人机料法环”的日常管理及异常的识别/反馈/处理。
- “改善” 即持续进行改善,更有效地利用现有的人、机、料,让员工能更轻松、更安全、更有效地工作,同时在交货期内生产出客户所需要的优质产品。
作为一线管理者,要在交期内生产客户需要的优质产品,就需要不断提高生产效率。作业改善是提高生产效率的非常有效的方法之一!一线主管作为作业改善的核心推动者,是最了解现场作业的人,他们承担着现场改善的重任。TWI-JM工作改善,就是一线管理者将作业的内容进行细分研究,检讨删除不必要的部分,合并或重组必要的部分,以便形成更有利的顺序,简化作业流程。它是一线管理者推动现场作业改善的重要方法。TWI-JM工作改善通过对作业现状中每一个细节的分解,使用5W1H自问方法来发现问题,应用IE-ECRS手法从中构思新的作业方法,解决现场存在的浪费。最终实现有效利用现有的材料,机械,人员,消除浪费,降低成本之目的。TWI-JM工作改善的实施主要分为作业分解、自问细节、构思新方法、实施新方法四个阶段。作业分解是工作改善的第一步,通过作业分解,将现行作业的实际情况,正确、完整地加以记录,掌握与作业有关的所有事实,然后通过作业分解表将这些步骤与细节逐一完整地记录下来。
细节就是细小的事项,工作中的每个动作都可以成为细节。比如搬运作业、机械作业、手工作业及所有的检查、等待、落后于计划都是细节。
- 作业分解必须要在现场一边观察一边进行,单凭想象和假定是不能掌握事实真相的。
- 要决定将作业分解到哪一个范围,细节尽可能取小一些,并且要毫无遗漏地记录每一条细节,包括等待的动作等。
对所做的分解作业,必须对所有的细节都毫无遗漏地进行自问。如果在自问的过程中出现了改善的构想,可以将其全部记在分解表的“想法”栏。那么到底应该如何自问呢?这个时候我们一般会用到5W1H分析法:它的目的是什么?(当第1问不太清晰的时候,追问该细节的目的是什么?调查该细节是否有益,或者从品质等方面追寻细节的根本目的,是对第1问的补充)找到做这个细节最合适的人 (熟练度、经验、体力、职责等)需要注意的是,必须按照以上的顺序展开自问,以避免做无用功。如果第1问、第2问就存在疑问,说明很可能这个细节可以取消掉,那么后边的几问就变得没有意义了。第3、4、5问会得出哪里、何时、谁做更合适,不同的地点、时机、人员可能会对应不同的方法,因此第3、4、5问自问完了之后,再进行第6问的自问,思考用什么方法、有没有更好的方法才有意义。同时还需要对材料、机器、设备、工具、设计、配置、动作、安全、整理整顿等九个项目进行自问。对这些项目的自问,就是看看这些项目是否存在问题点,能否改善得更好。在进行5W1H分析的基础上,可以寻找工序流程的改善方向,构思新的工作方法,以取代现行的工作方法。我们一般会运用ECRS四原则,即取消、合并、重组和简化的原则,可以帮助我们找到更好的效能和更佳的工作方法。去除(E):就是能不做的就去除掉不做。再简单的作业也需要时间、精力,合并(C):有些作业、或者零件合并起来做,也可以提高效率,减少失误。简化(S):就是通过优化作业场地布置,通过设备、工具、工装等优化使作业变得更省力、更简便、效率更高。第三阶段和第二阶段是紧密相连的,两个阶段之间是什么关系呢?如图所示:构思出来新的方法当然是用来实施的,怎么实施呢?每一个新方法的实施都会影响到各个层级与部门,所以要想实施新方法,一定要得到相关层级与部门的理解与认可。这个阶段的我们也可以分为四个小的阶段进行:通常我们会将新方法编写为“作业改善提案书”的形式,以取得相关人员的理解与认可。第四阶段实施新方法里还提到“持续改善”,意思是即使一次改善过程考虑得再周全,也不可能是完美的,因为没有最好,只有更好!一次改善的完成并不意味着结束,而是下一轮改善的开始。
想学更多现场管理技能,到智胜现场学习平台学习吧!